PROCESS CONTROL SERVICE
All accredited chemical engineering curriculums require one or more courses on industrial process controls. This is because it is vitally important to know how to correctly control processes to achieve the desired results as well as stay within a safe operating envelope. As most process engineers with a plant operations background can attest, it is hard to keep from gaining some hands-on process tuning and controls experience.
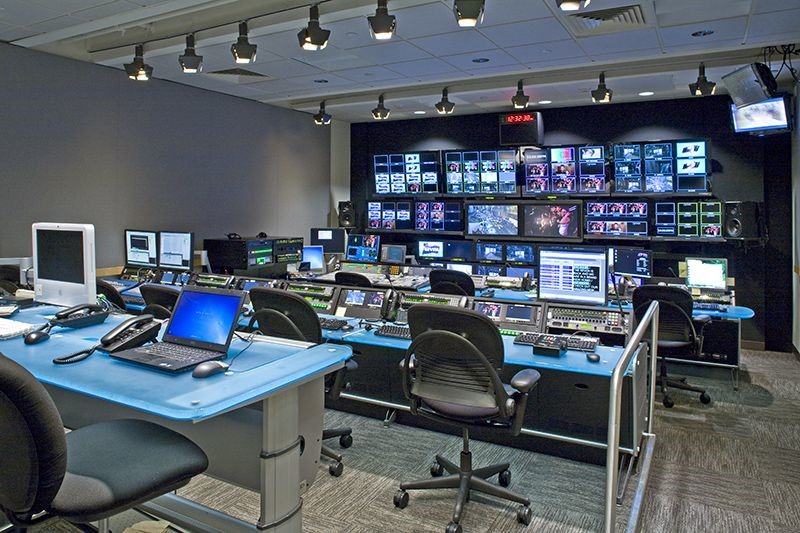
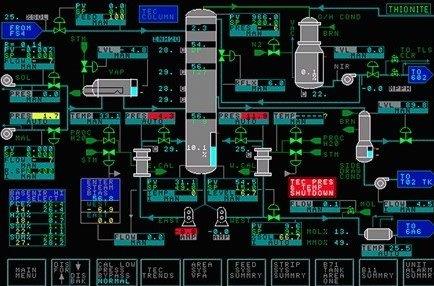
Some engineers like it so much they go on to develop a high degree of speciality in controls including control system training and administration, as well as installation and implementation. Many process engineers gain enough knowledge to design, specify, implement, and troubleshoot processes and control related systems.
This allows the engineer to gain vast instrumentation knowledge and configuration of the processes, including designing and testing safety interlocks that are vital to the processes. EBLprocess team is fortunate to have process engineers having the training, experience, and expertise to cover a very wide range of control and instrumentation needs.
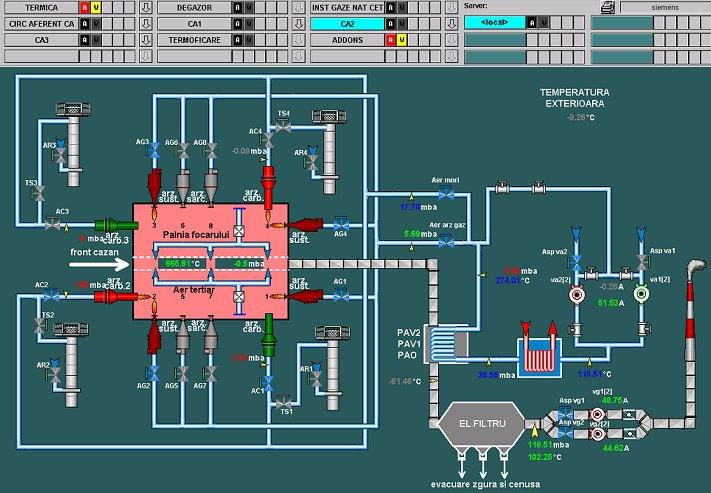
Becoming compliant with the ANSI/ISA 84.00.01-2004 Functional Safety: Safety Instrumented Systems for the Process Industry Sector standard can be a daunting task for a client. EBL Process teams has chemical process engineers with experience and training in the requirements within this OSHA Recognized and Generally Accepted Good Engineering Practice (RAGAGEP). ISA 84 revolves around all interlocks in the process. Safety Integrity Levels (SILs) are assigned to each safety function using a Layer of Protection Analysis (LOPA) or SIL Selection Analysis protocol. EBL Process team routinely provides training, guidance, and support in gaining knowledge and compliance with this standard.
EBL Process team has the capability as well as the expertise to assist in completing and facilitating each of these steps, including the assistance in on site interlock testing. The services are indicated below:
We routinely provide the following services on project we are assigned:
- Process control scheme development (as part of preliminary P&ID development)
- Process Control Description (PCD) documentation development
- Process instrument and control valve list
- Process instrument and control valve duty specifications
- Detailed final specifications for on-line analytic instrument analyzers
- Sizing of pressure relief devices and detonation arrestors.
In addition to the above items we can assist the detail design team by suggesting appropriate starting set points for alarms, interlocks, etc.They call it a ‘design team’ for a reason. In some cases, a level instrument vendor is best relied upon to specify exactly what type of measurement technique to use. In other cases, the client’s operations group will know best what types of devices to use based on years of experience. In some cases, our team or the detail design group may know that a measurement device is best suited for a given application. In other cases, only our team or another process group has the expertise to ensure that the entire loop (pump, pipe, valve, and measurement device) are all designed in such a way that the system hydraulics and functionality are correctly maintained across the system operating range.
We provide more detailed support of the control system for a process which we have designed if requested. This may take the form of the following:
- Distributive control system (DCS) technical bid package development and selection support
- Safety Logic Solver (SLS) design and selection support for Safety Instrumented System (SIS)
- Functional control system specification development.
We can collaborate with control system vendor engineers to help ensure that the operator interface screens are defined and laid out in such a way as to make monitoring and controlling the process as easy and logical as possible. It is best to put yourself in the shoes of the unit’s control room operator and carefully think through how the process will be monitored, controlled, alarmed, and reacted to in the middle of the night. EBLprocess engineers have years of experience supporting plant operations and can help ensure the control interfacing for new processes are very well defined from the first day of operation.
We have team of expertise who are specialized in tuning of controllers is something. The following are some of the services we provide:
- DCS proportional, integral, derivative (PID) control loop tuning
- Ladder logic programming for stand along programmable logic controllers (PLCs) or distributed control systems (DCSs)
- Function block programming for distributed control systems (DCSs)
- Structured text programming for distributed control systems (DCSs)
- SCADA (supervisory control and data acquisition) system tuning
- Personal computer (PC) based software control system tuning for smaller processes.
While most industrial processes are controlled by a series of independent PID control loops, some larger and more complex processes, such as integrated petroleum refineries, can benefit from the use of Advanced Process Controls, most commonly Multi-Variable Predictive Control (MVPC). EBLprocess has access to engineering resources with a great deal of experience using traditional PID controls, advanced PID controls, and MVPC. More importantly these engineers have learned enough to know when each is most appropriate. In general, simple control issues are best solved with simple tools to produce acceptable, repeatable, and reliable results. When a high level of process data integration may present opportunities for large economic impact then MVPC may be able to play an important role. Such is sometimes the case in large processes where changing upstream conditions can predictively be dealt with in the downstream processes to minimize off-spec product and maximize profits, i.e. a highly integrated refinery where changing crude feed composition will, whether highly-controlled or loosely-controlled, ripple throughout the entire plant.
As with most complex, custom design systems, the commissioning and startup of a new plant or unit is typically not without its share of problems. How many times have you seen?
- Control valve actions reversed
- Control valve positioner air supply valves closed
- PID controllers connected to the wrong valve in the field
- Automatic actions (i.e. interlocks) that do not trip as designed
- Etc?
EBLprocess engineers possessing both plant operations and process design experience are well qualified to help provide timely support during unit commissioning, testing, and startup. We have experience in supporting with Factory Acceptance Tests (FATs) and developing Site Acceptance Test (SAT) procedures that help minimize control discrepancies between design and commissioning. As required by ISA 84, we have prepared functional testing procedures that verify safety interlock operation that are performed prior to startup and during required periodic testing. We are comfortable working with plant operations management, operators, technicians, as well as with project contractors to help bring processes on-line in a safe and logical manner.
Most plant processes have safety interlocks that may or may not function reliably. Some clients may not be aware of interlock design that is embedded in their control system(s). We provide Cause & Effect Diagram/Matrix development and reviews by deciphering the client’s control system configuration to determine all the interlocks that are active in the process.
The ANSI/ISA 84.00.01-2004 standard for Safety Instrumented Systems is required by the OSHA PSM regulation. By becoming compliant with the ISA 84 standard, clients are gaining knowledge and tools to verify the reliability of safety instrumentation through the following services that EBLprocess provides:
- Training personnel and management on the ANSI/ISA 84.00.01-2004 standard, as well as its importance and requirements
- Developing or updating Cause & Effect Diagrams/Matrices – with field instrumentation and control system review, if necessary
- Performing LOPA or SIL Selections Analysis for the Safety Instrumented Functions (SIFs)
- Gathering instrumentation and control system data to verify interlock reliability
- Recommending and designing reliable interlocks, from the SIS control system to the interlock instrumentation
- Developing functional testing documents and assisting with the periodic testing protocol.
Most industrial process plants, if they are successful and safe, end up evolving to take advantage of newer technologies and to meet ever-increasing market and regulatory demands. Part of this evolution is the need to control and safely interlock the processes more precisely and more reliably. Upgrading the controls and safety instrumentation of an existing plant unit or major unit operation often involves a combination of skills such as investigation, data collection and analysis, troubleshooting, design, specification, functional testing, startup, and optimization. EBLprocess senior level process design engineers with plant operations experience are well suited for such work.
If your facility employs the use of process control or automation, you will benefit from Software Requirements System (SRS) analyses! While PSM covered processes are regulated under ISA 84, industry best practice standard is moving very quickly towards all-encompassing employment of SRS analyses for control systems.
Typically, the timeline goes as follows:
- A SIL Selection is conducted on-site with members including, but not limited to, process engineers, design engineers, maintenance, and operations to determine the SIL rating for the various process controls and interlocks.
- Equipment information is collected for the various control systems for analysis
- Calculations are run utilizing the reliability data to quantify the base case SIL rating of the equipment
- Based on the results, recommendations that can be various in nature that can include but are not limited to equipment specifications, interlock testing frequency, equipment lifetime, maintenance practices, and equipment redundancy are made to assist in achieving targeted SIL ratings
- Testing Documents for each interlock are developed for use in the field and to keep as a record
- At each scheduled shutdown, interlocks are tested and verified according to the testing documents
Here for you
Call us 24/7. We are there for your support
GPS Address
AK - 040-4605
Contact Details
Email Address: [email protected] +233200642591 +233202473696
Where to find us
119 Otumfo Osei Tutu II
Adjacent SSNIT Buidling
Kumasi - Ashanti Region
Ghana, West Africa